Maintaining a controlled temperature in manufacturing facilities is crucial for optimal performance. Excessive heat can lead to equipment malfunctions, reduced productivity, and an uncomfortable working environment for employees. Effective heat extraction systems ensure that machinery operates efficiently and workers remain comfortable, especially during the hotter months.
Implementing a robust heat extraction system not only safeguards equipment but also boosts employee morale and productivity. It creates a safer, more comfortable workspace, ultimately leading to higher quality products and operations efficiency.
Challenges Faced by the New South Wales-Based Manufacturer
A New South Wales manufacturer produces high-quality plastic containers using materials like polyethylene terephthalate and high-density polyethylene. Their capabilities include extrusion blow moulding and injection stretch blow moulding, allowing them to make containers up to 5 litres. They also offer a wide range of caps, closures, and labelling services for various bottle types.
The factory faced major ventilation issues after removing its previous heating and cooling extraction system. Airflow became inadequate, particularly during summer. Existing extraction fans were scattered unevenly, creating an inefficient system that couldn’t effectively remove heat from the machinery. To prepare for the warmer months, the company needed a solution to reduce heat and improve air circulation across key production areas.
Fanquip’s Tailored Heat Extraction Solution
After thorough site visits and assessments, a tailored ventilation system was designed to meet the facility’s specific needs. New filtered roof supply fans were installed in high-heat areas to improve air circulation, lower internal temperatures, and create a more comfortable workspace.
The system also ensured fresh, filtered air flowed consistently throughout the facility, maintaining optimal air quality. This customised solution effectively addressed the manufacturer’s requirements, improving heat extraction and air quality to support workforce health and productivity.
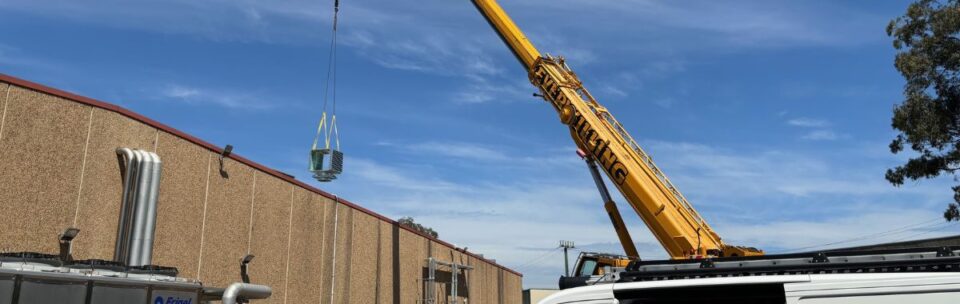
Key Design Features and Implementation Process
The design and implementation of the new ventilation system included several key features:
- Removal of Existing Ducting: Clear existing roof ducting to make way for the new fan units and optimise airflow.
- Installation of Filtered Roof Supply Fans: Two 800mm filtered roof supply fans were installed, positioned for maximum effect over high-heat areas.
- Custom Curb Base Mounts: The fans were mounted using specially designed curb bases compatible with the existing square extrusion on the roof.
- Structural Support Installation: Purlin trimmers were added as necessary to reinforce the installation points.
- Electrical Wiring & Control Setup: Each fan was wired to the main electrical board with 20–30 metres of cabling per fan, allowing centralised control via a single switch to operate both fans simultaneously.
- Installation Support: Hired Elevated Work Platform and crane services ensured safe and efficient installation of the fan units.
These steps ensured the system was installed efficiently and safely, providing the necessary structural support and electrical integration for optimal operation.
Ensuring a Summer-Ready Facility with Filtered Roof Supply Fans
Fanquip Filtered Roof Supply Fans are durable, weatherproof axial fans designed for clean air delivery in industrial and commercial spaces, especially where ceiling height limits traditional filter boxes.
Each fan has a fully welded mild steel casing with a hot-dip galvanised finish for weather resistance and longevity. Adjustable pitch impellers, made of GRP or cast aluminium, ensure optimal air performance. The fans also feature mild steel weatherproof louvres on up to four sides, coated with polyester powder for protection, and include hinged doors for easy maintenance access.
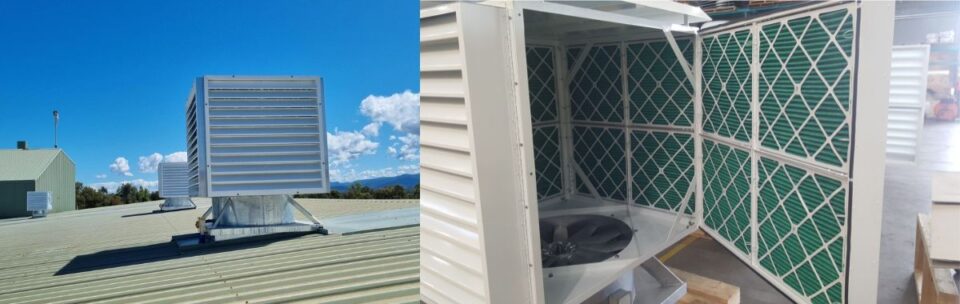
Ready to prepare your facility for summer?
Let us know your needs, and we’ll recommend a range of products tailored to your requirements.